or So what exactly is combustion energy and heat transfer anyway?
This article is based on more than 30 years of field testing, measuring, and auditing equipment performance. Although some of the information requires interpretation, it’s still based on proven field performance.
What is Combustion Energy?
Combustion is the burning of some kind of fuel — whether it’s natural gas, propane, oil, coal, or wood — to produce usable heat or energy. This energy, in turn, transfers, at first, to a device like a heat exchanger. The exception: when combustion flames and gases make direct contact with whatever needs to be heated. This article examines how to maximize the usable energy from a fuel source and how to transfer that source through a heat exchanger to air or water.
For simplicity, let’s cover two main types of energy: potential energy (fuel) and kinetic energy (thermal energy).
Potential energy is the most energy stored that must convert to usable energy (kinetic energy). Converted kinetic energy, through heat transfer, becomes thermal energy.
For example: A cubic foot of natural gas may contain a potential energy of 1,000 Btu per cubic foot, a gallon of propane may contain a potential energy of 90,000 Btu per gallon, and a gallon of oil may contain 140,000 Btu of potential energy.
Until converted through combustion, none of the energy these fuels store is available for any useful heating process.
So, potential energy needs to convert to thermal energy through combustion. Then, the thermal energy contained in the flame and combustion gases can transfer to a cooler object by heat. In heating, the cooler object is the heat exchanger, but, it’s not the only object that will absorb heat. Even so, the heat exchanger now contains a percentage of thermal energy that is available and then transfers this energy to air or water. If this seems complicated, well, it is — and it isn’t.
A proper combustion process burns 99.99% of the fuel, which should equal the amount of thermal energy or Btu released from the potential energy of the fuel for transfer to the heat exchanger. We assume this and use it to calculate the operating efficiency of equipment. But, is this what it appears to be? Is it possible for this thermal energy to transfer or absorb into something other than the heat exchanger? Besides the heat exchanger, where could this thermal energy go?
Perfect Combustion?
Natural gas can have a potential energy of 1,000 Btu per cubic foot, as stated earlier. To convert to 100% thermal energy and only transfer this energy to the heat exchanger, natural gas must burn at perfect combustion (stoichiometric) with no excess air (0% O2) to produce a flame temperature around 3,600°F.
Suppose perfect combustion was attainable. How much cooler would the flame temperature and combustion gases have to be before exiting the heat exchanger for 100% energy transfer? The answer: about 70°, or the temperature of the combustion air used. But, is the heat exchanger the only thing that can absorb this heat? At 0% O2, the answer is yes. But, that’s not the normal O2 content of the combustion gases.
A good O2 level in residential furnaces is about 6%, which produces a flame temperature around 2,800°. This means 800° of thermal energy was already exchanged or lost before any energy was transferred to the heat exchanger. Where does it go?
When discussing oxygen, we’re talking about air. But, air contains about 79% nitrogen (N) and only 21% oxygen. Nitrogen, which is often ignored, is a thief that absorbs heat or dilutes it. At 6 percent O2, there would also be around 24% nitrogen, which steals the 800° for itself.
What Does A Cup of Joe Have to do with Combustion?
Example 1: A full cup of coffee (fuel) at 180F brings the cup (heat exchanger) to 180F. Adding six drops of cream (oxygen and nitrogen) lowers the temperature to 127.5F. The cream solution absorbed 30% of the heat, disqualifying it from being exchanged to the cup.
A simple way to explain this: Consider a cup of coffee with cream and water added.
Coffee = Fuel
Cup = Heat Exchanger
Cream = O2
Water = N
A coffee cup contains 100% coffee (50 drops) at 180° and is almost full to the brim. Coffee is the thermal energy and the cup is the heat exchanger. At 180°, the coffee contains 100% of its thermal energy, which would be able to bring the whole cup temperature up to about 180°.
That might burn our hands. We have a little room in the cup, so we add some cream that is 40° (let’s say six drops) to cool it down. With those six drops of cream, 24 drops of water tag along. That makes the coffee 127.5° and most of the cup approximately 127.5°. The same amount of thermal energy is in the cup, but 30% of it was absorbed by the water and can no longer be exchanged to the cup.
Example 2: When 12 drops of cream (oxygen and nitrogen) are added into the 180F coffee (fuel), it drops the temperature to 103.6F, which means the cup (heat exchanger) can only reach 103.6F.
Let’s change our coffee scenario a bit. We’re in a restaurant and our coffee is too hot. So, we tell our waitress. She’s having a bad day, so she dumps 12 drops of cream into our coffee, which increases the drops of water to 48. Now, our coffee is only 103.6° and lukewarm. But it’s the hottest the cup (heat exchanger) can get. Therefore, 103.6° is the hottest the cup (heat exchanger) can get.
At this point, we assume the cup is full, so it would be about the same temperature from top to bottom. But, what if the cup was only 60% full when the 12 drops of cream and 48 drops of water were added? That means 40% of the cup is barely heated at all.
Assuming air or water is flowing past the cup (heat exchanger) versus us holding it with our hand, the cup is under-performing.
Temperature as an Indicator
Temperature is an indicator of how many Btu (thermal energy) a substance contains. At 6% oxygen, the flame temperature is 2,800°. This is 800° less than 3,600°, meaning less available Btu to transfer to the heat exchanger. I estimate about 90% of total thermal energy produced is available to transfer to the heat exchanger.
What if the oxygen content is 12%? That would put the flame temperature at 2,000°, which is even less thermal energy to transfer. Now, my estimate is approximately 80%. So, how can a furnace be 80%-plus or 90%-plus efficient if the available thermal energy of combustion is only 80%?
This exercise shows only a certain amount of available thermal energy is transferred by the process defined as heat. The combustion process creates two types of heat: sensible heat and latent heat. All fuels contain carbon (C) and hydrogen (H). Most fuels, including natural gas, are initially given two Btu values: higher heating value (HHV), and lower heating value (LHV), based on the carbon and hydrogen content.
Natural gas is 90% carbon and 10% hydrogen. In the combustion process, carbon combines with oxygen and produces carbon dioxide (CO2) or sensible heat. So, a cubic foot of natural gas rated at 1,000 Btu potential energy contains 900 Btu of carbon and 100 Btu of hydrogen. During combustion, hydrogen combines with O2 and produces H2O or latent heat.
But, because hydrogen now combines with O2, the percentage of latent heat is 18% at perfect combustion (stoichiometric) or 0% O2. At 6% O2, the latent heat volume is closer to 14% and puts the sensible heat volume at 86%. If you have a non-condensing furnace, what is the maximum sensible heat available at normal combustion? Answer: Less than 90% with 6% O2.
Two Questions
Here are two questions to ask following the first part of our discussion: First, when discussing Btu input of a heating appliance, what is more important, the cubic feet of natural gas, the gallons of propane or oil we are supplying, or the actual amount of thermal energy produced and available for transfer by the fuel through the combustion process?
Second, does combustion analysis provide us the best means to maximize the amount of thermal energy produced? No, it doesn’t consider enough data, even though combustion analysis is the industry norm.
What is Combustion Heat Transfer?
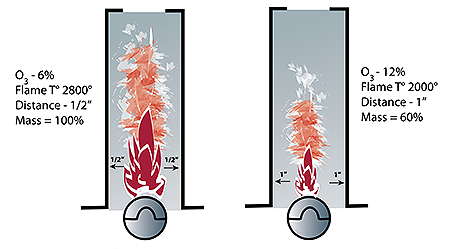
Figure 1: The distance between a flame and the heat exchanger greatly impacts the equipment’s ability to transfer heat.
Heat transfer is the exchange of thermal energy from a hotter substance to a cooler substance. This is done by radiation, convention, or conduction, with radiant heat being the most efficient. When reading technical articles on heat transfer, three things are always listed as contributors: temperature, mass, and specific heat capacity (heat exchanger). Recently, I realized there are two other important factors: line of sight and residence time.
Temperature, by definition, is the measure of approximate thermal energy (Btu) of the molecules of a substance. The hotter the substance (flame temperature), the more thermal energy is available for exchange.
When we discussed energy, we mentioned three different flame temperatures: 3,600° (perfect combustion), 2,800° (at 6% O2), and 2,000° (at 12% O2). Inside the heat exchanger, where the flame exists, radiant heat is the main method of energy transfer.
Radiant heat increases or decreases to the fourth power of its absolute zero (Rankine), according to the Stefan-Boltzmann Law. What does this mean? Okay, I guess I have to include just a little scientific jargon. How does this affect convective or conductive heat?
When reading technical articles on heat transfer, three things are always listed as contributors: temperature, mass, and specific heat capacity (heat exchanger). Recently, I realized there are two other important factors: line of sight and residence time.
If you increase the temperature of a flame or surface from 2,000° to 2,100°, there would be about a 6.7% increase in convective or conductive heat to or from the heat exchanger. However, the most important place is at the flame within the heat exchanger, where most of the heat transfer is radiant.
More on Temperature and other Heat Transfer Requirements
You would find similar discussions on this from manufacturers’ technical data on radiant heaters. Now, looking at the same increase of 100°, there is an increase in the radiant heat transfer of 22 percent, according to Stefan-Boltzmann. What do you think happens when the flame temperature increases from 2,000° to 2,800°? For radiant energy to be most effective, hotter is better.
Therefore, temperature is the first requirement for maximum heat transfer. A second requirement is that the flame has to be big enough or have mass.
For example, a candle burns at approximately 2,500°. If you put a candle in a furnace heat exchanger, it doesn’t heat very well. The candle may be hot enough, but it’s not big enough. The flame and the gases of combustion must be of a certain mass to effectively heat the volume of the heat exchanger surface. Therefore, flame size and combustion gas quantity produced inside the heat exchanger should be whatever size or mass is necessary to produce the rated output of the equipment.
This does not mean to keep increasing gas pressure or orifice size or over-fire the equipment. It means adjusting equipment with a combustion analyzer to verify safe operation and create the necessary temperature (Btu) and mass to deliver the Btu output listed on the manufacturer’s rating plate.
Usually, the third requirement for heat transfer is heat capacity, which is determined by the design of the heat exchanger and its ability to absorb and dissipate thermal energy.
A deterrent that would affect the heat capacity of a furnace heat exchanger is soot. On a boiler or water heater, it would be scale. These deterrents greatly reduce the ability of the heat exchanger to absorb heat. This reduces heat capacity.
Another deterrent is when a heat exchanger cannot transfer the heat it absorbs. On forced-air equipment, this issue involves proper airflow. On a boiler, this involves pump flow. These would fall under the category of residency time on the delivery side of the heat exchanger. Delta T and flue temperature are measurements that should tell you if you face any of these issues. Unfortunately, without knowing how to interpret the real factors of heat transfer, many look at delta T and flue temperature as a fuel indicator and make wrong decisions.
Line of Sight
A fourth factor impacting heat transfer is line of sight or proximity. A continuation of the Stefan-Boltzmann Law to explain this would be radiant heat intensity varies as the square of the distance from the heat source. A simpler way to say this: The closer a flame is to the heat exchanger, the more heat radiates. Although the flames in Figure 1 are the same size and temperature, their distance from the heat exchanger will greatly affect their abilities to transfer heat. If the flame temperature on the right were also cooler, the difference in heat transfer would even be greater.
Those familiar with proper equipment testing already have a decent understanding of these principles. Choosing to ignore these principles leads to poor, unsafe, and inefficient operation of HVAC systems.
The final factor, again, now on the inside of the heat exchanger, is residence time. No matter how big or how hot the flame or gases, the amount of time making contact with a median is quite important. A bonfire can be big and hot, but if you ride your bicycle past it, you hardly feel the heat versus standing in front of it. You can swipe your hand right through a candle flame and feel nothing.
Temperature, mass, heat capacity, and line of sight can all be sufficient, but too little contact time or residency nullifies their effects. On the fire side, or inside a heat exchanger, draft or flow pressure determines contact time. On the outside of the heat exchanger, airflow or pump flow determines the contact time.
Only a combustion analyzer and proper combustion diagnostics determines if all the above are correct, safe, and efficient and conform to the equipment’s listed rating. Determining true performance of mechanical equipment and adjusting them properly requires measuring their output.
Those familiar with proper equipment testing already have a decent understanding of these principles. Choosing to ignore these principles leads to poor, unsafe, and inefficient operation of HVAC systems.